Cold process soap separating is a common issue that soap makers may encounter during the soap making process. It occurs when the soap batter, after being poured into the mould, decides to separate and form little oily pockets or a layer of oil on top of the soap. This separation can be frustrating and disappointing, as it renders the soap unusable in it’s current state. To salvage the soap, you’ve two options: you can either tip the soap out of the mould and re-mix the batter, or you can wait and see if the separation re-absorbs. However, if the separation doesn’t re-absorb, it’s crucial to address the issue promptly to prevent any further complications.
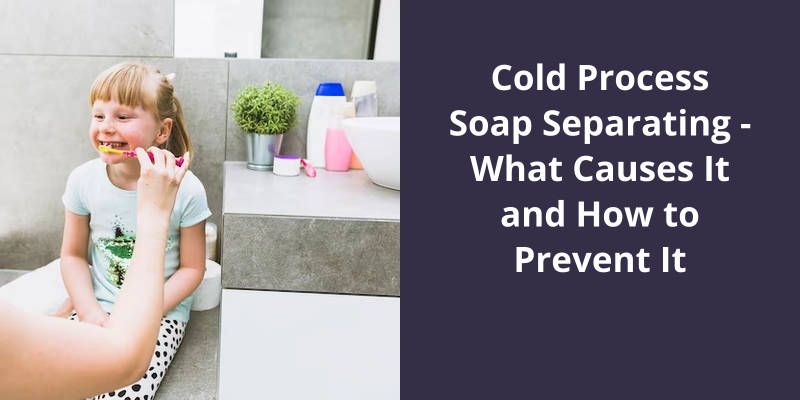
What Does Separated Soap Look Like?
Separated soap is visually distinct, as the fragrance oil fails to incorporate into the soap batter, resulting in noticeable oil slicks that start to pool on top of the mixture. These pools resemble the appearance of butter atop a bowl of cream of wheat. The separated soap exhibits a striking contrast between it’s smooth, creamy base and the visible layer of oil that accumulates on it’s surface.
Separation is often mistaken for another soap-making issue called ricing, as the two problems may occur simultaneously. Ricing involves the formation of small, grain-like clumps in the soap batter, giving it a rice-like texture.
To prevent separation during the cold process soap-making method, there are several measures that can be taken. First and foremost, ensuring the soap ingredients, including the fragrance oil, are at the appropriate temperature is crucial. Cold ingredients make it difficult for the fragrance oil to blend smoothly, leading to separation.
Additionally, incorporating the fragrance oil gradually and in small increments while stirring continuously can help prevent separation. This allows for better dispersion and integration of the fragrance oil into the soap batter, reducing the likelihood of separation. Careful attention to the consistency and temperature of the soap batter throughout the mixing process is also essential to prevent separation.
Whether you’re a seasoned soap maker or just starting out, you may wonder if cold process soap can be remelted. The good news is that it can! Rebatching cold process soap involves melting it down and pouring it into molds, allowing it to harden before cutting it into desired shapes. This process allows you to salvage any fragrances, colors, or additives that may have been lost during the initial soap making process, giving you the chance to create unique and personalized soaps.
Can Cold Process Soap Be Remelted?
Rebatching cold process soap is a great way to salvage a batch that didnt turn out quite as planned. While traditional cold process soapmaking involves mixing oils and lye to create soap from scratch, sometimes things don’t go according to plan and the soap ends up separating. This can leave you with a batch of soap that’s visible oil pockets or a grainy texture. But fear not, because this soap can be remelted and rebatched to create a new, usable product.
The process of remelting cold process soap is relatively simple. All you need to do is cut up the soap into small chunks and melt it down using a double boiler or microwave. Once the soap has melted, you can add in any additional ingredients or scents that you want before pouring it into suitable moulds. After the soap has cooled and hardened, it can be cut into bars or shapes, just like any other cold process soap.
By remelting the soap, they can create a new batch with a smoother texture and more consistent appearance. Additionally, rebatching can be a great way to experiment with different scents and additives, as you can easily add them in during the remelting process.
These resources often offer step-by-step instructions, troubleshooting advice, and creative ideas for creating unique soap designs. However, with some experimentation and creativity, you can often achieve a beautiful and usable final product.
With some patience and practice, you can turn a failed batch into a unique and beautiful soap creation.
Benefits of Rebatching Soap Versus Starting From Scratch
- Cost-effective: Rebatching soap allows you to reuse leftover soap scraps, reducing waste and saving money on purchasing new ingredients.
- Preserves beneficial properties: When you rebatch soap, you can retain the natural oils and additives present in the original soap, preserving their benefits for your skin.
- Customizable options: Rebatching gives you the freedom to add your preferred scents, colors, and additional ingredients, allowing for personalized soap creations.
- Time-saving: Compared to making soap from scratch, rebatching requires less time and effort since you’re starting with a pre-existing soap base.
- Reduced risk: As rebatching uses pre-made soap, it eliminates the need for handling potentially dangerous lye, making it a safer option for those who prefer to avoid it.
- Experimentation: Rebatching soap allows for experimentation with different soap recipes and combinations, enabling you to create unique blends that suit your preferences.
- Eco-friendly: By reusing soap scraps and minimizing waste, rebatching contributes to a more sustainable and environmentally friendly approach to soap making.
Source: How to Rebatch soap scraps and off cuts
Soap separation can be a frustrating problem, but luckily there are some simple solutions. If you notice your soap starting to separate after pouring it into the mold, don’t worry! One option is to carefully pour the soap back into your mixing container and stir or blend until it reaches a true trace. Alternatively, you can try hot processing the soap by scooping it into a slow cooker. These methods can help you salvage your soap and achieve the desired consistency.
How Do You Fix Soap Separation?
Soap separation, also known as soap curdling, can be a common issue that soapmakers encounter during the cold process soapmaking method. It can be frustrating to see all your hard work going down the drain, quite literally. However, there are solutions to fix soap separation and prevent it in the future.
The first solution to fix soap separation is to pour the separated soap back into your mixing container. By doing so, you can stir or blend it until a true trace is reached again. This will help to recombine the separated ingredients and create a more stable soap mixture.
Another solution is to scoop the separated soap into a slow cooker and utilize the hot process soapmaking method. Heat acts as an accelerator and can help to reintegrate the separated ingredients. This method is especially useful when dealing with larger batches of soap.
Fragrance oils or essential oils that contain high levels of vanillin can lead to separation due to their chemical composition. Using stabilizers or additives specifically designed to prevent soap separation can be a useful preventative measure.
Lastly, considering the temperature and environment during the soapmaking process is crucial. Maintaining a stable temperature and avoiding sudden fluctuations can help prevent this issue.
Fixing the issue at hand and taking the necessary steps to prevent it in the future will ensure that your cold process soapmaking journey runs smoothly, resulting in beautiful, stable bars of soap that you can be proud of.
Common Causes of Soap Separation and How to Avoid Them
Cold process soap separation, also known as soap “ricing,” occurs when the soap mixture starts to separate into solid and liquid components. This can happen due to various reasons, but some common causes include:
1. Temperature: Soap separation often occurs when the temperature of the soap mixture drops too quickly. To prevent this, ensure that the soap mixture is kept at a consistent temperature throughout the curing process.
2. Ingredients: Certain ingredients, such as fragrance oils or essential oils, can accelerate soap separation if they aren’t compatible with the soap recipe. Make sure to choose ingredients that are suitable for cold process soap making.
3. Mixing Technique: Inadequate mixing can also lead to soap separation. It’s crucial to thoroughly mix all the ingredients during the soap making process to ensure proper emulsification and prevent separation.
To avoid soap separation, follow these preventive measures:
1. Control Temperature: Maintain a steady temperature during the curing process by using a soap heating pad or insulation if necessary.
2. Test Ingredients: Before adding any fragrance oils or essential oils to your soap recipe, perform a small test batch to check for compatibility and potential separation issues.
3. Mix Thoroughly: Take your time to mix all the ingredients, ensuring that they’re fully incorporated. Use a stick blender or hand whisk to achieve a smooth, homogeneous mixture.
By paying attention to these factors and following the prevention methods, you can minimize the risk of cold process soap separation and create a beautiful, stable soap.
Now that we’ve learned how to prevent soap layers from separating, let’s explore some additional tips and techniques to enhance the visual appeal and longevity of your handmade soap creations.
How Do You Keep Soap Layers From Separating?
When making cold process soap, one common issue that soapmakers often encounter is the separation of soap layers. This occurs when the soap mixture starts to separate into distinct layers instead of remaining cohesive. It can be frustrating to see all your hard work go to waste as the layers disintegrate. However, by implementing a few precautions, you can prevent this from happening and achieve beautifully layered soap bars.
One effective method to keep soap layers from separating is to spritz each layer with alcohol just before pouring the next layer on top. Alcohol acts as a bonding agent, helping to “glue” the layers together and preventing them from separating. Additionally, alcohol also aids in eliminating bubbles, ensuring a smooth and flawless finish to your soap bars.
Moreover, properly insulating your soap mold can help maintain a consistent temperature throughout the soap-making process. Uneven cooling can contribute to layer separation, so insulating the mold with towels or blankets helps promote a more even distribution of heat, preventing the layers from separating due to temperature fluctuations.
Furthermore, using additives like sodium lactate or salt can help prevent soap layers from separating.
Finally, when pouring your soap layers, ensure that each layer is poured gently and evenly. A smooth and gradual pour helps minimize disruption and turbulence that can cause the layers to mix or separate. By pouring carefully, you give the soap layers an opportunity to settle and fuse together, creating beautiful and unified designs.
Choosing the Right Oils and Fats for Soapmaking to Help Promote Cohesion in the Layers
Choosing the right oils and fats for soapmaking is crucial to prevent soap separation. Certain oils and fats contain properties that promote cohesion in the layers of cold process soap. These oils, such as coconut oil and palm oil, help the layers to bind together and prevent separation. By carefully selecting the appropriate oils and fats for your soap recipe, you can ensure a cohesive and beautifully layered cold process soap.
Allowing your soap to fully cool and harden before cutting is crucial in preventing the layers from separating. While it may be tempting to start cutting earlier, the patience will pay off in the end. The cooling and hardening process can take a few hours, depending on the size of your project.
Why Are My Soap Layers Separating?
Another factor that can cause soap layers to separate is an imbalance in the formulation. When the ratio of oils to lye isn’t properly calculated, it can lead to an unstable soap that’s a higher tendency to separate. To prevent this, it’s important to accurately measure and weigh the ingredients and follow a reliable soap recipe.
The temperature at which you add fragrance or essential oils to your soap can also contribute to separation. It’s recommended to allow both the oils and soap batter to cool down to a similar temperature before combining them.
If the oils and lye aren’t thoroughly mixed together, it can create pockets of unmixed ingredients that may separate during the saponification process. Make sure to mix the oils and lye solution until they reach trace, a stage where the mixture begins to thicken.
Lastly, the curing process plays a crucial role in preventing soap separation. Allowing the soap to cure for a sufficient amount of time, typically four to six weeks, allows for the water content to evaporate and the soap to harden. This helps to minimize the risk of layer separation and ensures a more stable and long-lasting bar of soap. Patience is key when it comes to curing your soap, as rushing the process can lead to unwanted separation.
How to Troubleshoot and Fix Soap Separation Issues
- Check the temperature of the soap mixture.
- Make sure you’re using the correct ratio of oils and lye.
- Mix the oils and lye together thoroughly.
- Avoid overmixing or undermixing the soap.
- Consider using a hand mixer or stick blender to ensure proper emulsion.
- Check the age and quality of your oils and lye.
- Store your soap in a cool, dry place.
- Consider adding additives or stabilizers to prevent separation.
- Experiment with different soapmaking techniques or recipes.
Conclusion
However, understanding the causes and implementing preventive measures can help minimize the occurrence of separation. Factors such as temperature, fragrance oils, additives, and recipe formulation play a significant role in this issue. By ensuring proper temperature control, using fragrance oils that are compatible with the soap base, carefully selecting and incorporating additives, and formulating recipes with suitable ratios of oils and lye, soap makers can greatly reduce the risk of separation. Additionally, techniques such as stick blending and hand stirring can be employed to promote a more thorough emulsion. However, in the event that separation does occur after moulding, it’s essential to assess whether the soap will reabsorb the separated oils or not. If not, it’s important to take prompt action, either by tipping out the soap and remixing the batter or considering the separated portion unsalvageable.