The maximum temperature required for steam distillation is typically around 100 degrees Celsius or 212 degrees Fahrenheit. This is because steam distillation involves the process of heating a mixture to create steam. This steam then carries the volatile substances to a cooling area where it condenses back into a liquid. The temperature is essential to create enough steam without adversely affecting the substances to be distilled. However, it’s important to note that the ideal temperature can vary based on the specific properties of the substance being distilled.
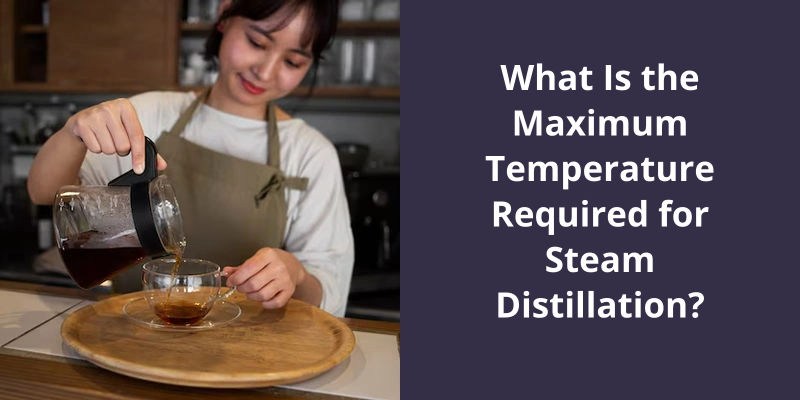
What Are the Requirements for Steam Distillation?
Steam distillation is a highly effective and versatile technique used to extract essential oils and other valuable compounds from organic materials. To use steam distillation effectively, there are several key requirements that must be met. First and foremost, the substance to be extracted must have a boiling point higher than that of water, as steam distillation relies on boiling the material to release it’s volatile compounds. If the material to be extracted can’t be heated to that temperature because of it’s susceptibility to decomposition or other unwanted reactions, then steam distillation may be a viable alternative.
This can be accomplished using a steam generator or a boiler that’s designed for this purpose. It’s essential that the steam be of sufficient pressure and temperature to properly heat the material and extract the desired compounds without causing damage or degradation.
Proper equipment is also crucial for steam distillation, including an appropriate still or distillation apparatus that’s capable of withstanding high temperatures and pressures. The type of apparatus used will depend on the size and nature of the material to be extracted, as well as the specific requirements of the application.
In addition, the starting material must be properly prepared and loaded into the still. This may involve grinding, chopping, or otherwise breaking down the material into smaller pieces that can be easily handled and heated. It’s also important to ensure that the material is properly cleaned and free from contaminants that could affect the quality or purity of the extracted compounds.
Finally, it’s important to carefully monitor the steam distillation process and make any necessary adjustments to ensure optimal performance. This may include adjusting the steam flow rate or temperature, or making changes to the design or operation of the distillation apparatus.
Maintaining the optimal temperature for steam distillation is a key factor in ensuring successful extraction of essential oils. The temperature range needs to be carefully monitored to prevent any unwanted results. In the next section, we will explore the importance of water and it’s role in steam distillation.
How Does Temperature Affect Steam Distillation?
The temperature not only determines the efficiency of the process but also affects the quality of the end product. For example, when extracting essential oils from plant materials, the ideal temperature range is between 60-100°C as this allows the oil to vaporize without decomposing or oxidizing. At this temperature range, the extraction process is efficient and abundant, resulting in high yields of essential oil.
In contrast, when the temperature is too high, the harsh conditions can damage the delicate chemical compounds present in the plant material, such as terpenes. As a result, this can affect the aroma, flavor, and potency of the essential oil. On the other hand, if the temperature is too low, the essential oils may not be fully extracted as the vapor pressure wouldn’t be sufficient to carry the oil out of the plant material.
To maintain the correct temperature range during steam distillation, it’s essential to have precise control of the heat source and heat transfer mechanism. This can be achieved by using a temperature controller, which adjusts the heat accordingly, or by using a water bath to provide a stable temperature environment for the distillation apparatus.
Moreover, the type of plant material being distilled also plays a crucial role in determining the optimal temperature range for steam distillation. In contrast, some plant materials like eucalyptus or cloves need a higher temperature range (around 100°C) to vaporize the compounds fully.
It ensures the efficiency and quality of the extraction process and determines the composition of the end product. By understanding how temperature affects steam distillation, one can carry out the process with precision and produce essential oils of exceptional quality.
Now that we know how the boiling point of a liquid is determined through simple distillation, let’s explore the different applications of this technique in various industries.
What Is the Temperature for Simple Distillation?
Simple distillation is a technique used to separate a liquid from a mixture based on differences in boiling points. Typically, a mixture is heated in a flask and the vapors are condensed and collected in a separate container. The temperature range at which the distillate is collected is the observed “boiling point” for the liquid. It’s important to note that other factors such as atmospheric pressure and impurities in the mixture may affect the observed boiling point.
When carrying out a simple distillation, it’s important to select a suitable temperature range for collecting the distillate. The temperature range should be narrow enough to ensure that only the desired compound is collected, but wide enough to allow for a reasonable yield. The temperature range for simple distillation can vary depending on the compound being distilled. For example, water usually distills in the boiling point range of 99–101 °C, whereas ethanol boils at around 78 °C.
To ensure accurate temperature measurement during distillation, a thermometer is usually inserted into the distillation apparatus. It’s important to note that the thermometer shouldn’t be in contact with the boiling liquid as this may affect the accuracy of the temperature measurement.
In addition to temperature control, other factors such as heating rate and stirring rate may affect the efficiency of the distillation process. It’s important to optimize these variables to ensure the highest possible yield of the desired compound. For example, a slow heating rate may be more effective for separating compounds with a narrow boiling point range, whereas a fast heating rate may be more effective for separating compounds with a wider boiling point range.
Water usually distills in the boiling point range of 99–101 °C. Accurate temperature control is essential for the efficient separation of compounds by distillation.
How Does Atmospheric Pressure Affect the Boiling Point in Simple Distillation?
Atmospheric pressure affects the boiling point in simple distillation as a higher pressure means more energy is required to vaporize the liquid, resulting in a higher boiling point. Conversely, lower atmospheric pressure means less energy is required to vaporize the liquid, resulting in a lower boiling point.
The significance of temperature control in distillation can’t be overstated. It’s a direct impact on the quality, optimization, stability, safety, and energy costs of the distillation process. Even though it may appear as a straightforward aspect to manage, a deeper understanding is needed to make certain that a distillation column is operating at it’s optimal level. Therefore, delving into the importance of temperature measurement is vital to ensure the optimum distillation performance.
Why Is Temperature Important in Distillation?
When it comes to distillation, temperature plays a crucial role in achieving the desired end product. Temperature affects not only the chemical and physical properties of the components being separated, but it also determines the efficiency of the process. In order to achieve optimum product quality, temperature control must be carefully monitored and managed throughout the distillation process.
Different components have different boiling points and vapor pressures, which means that they’ll evaporate and condense at different temperatures. By carefully controlling the temperature, it’s possible to separate the desired product from other components, effectively purifying it.
By monitoring the temperature at different points in the distillation column, operators can adjust the process to ensure that all components are being separated as efficiently as possible. This can result in a more streamlined process that requires less energy and produces less waste.
High temperatures can create volatile environments that can be hazardous to workers and equipment. By carefully controlling the temperature, plant operators can ensure that the process remains stable and safe, reducing the risk of accidents and equipment damage.
By carefully monitoring and managing temperature throughout the process, operators can achieve greater efficiency, improved product quality, and greater safety, ultimately leading to a more profitable and successful operation.
Now that we’ve established that superheated steam can indeed be over 100 degrees, let’s delve deeper into the topic and find out more about it’s properties and applications. From industrial processes to power generation, superheated steam has a range of practical uses that make it an essential component in many modern systems. So, let’s explore the fascinating world of superheated steam and it’s significance in various industries.
Can Steam Be Over 100 Degrees?
Steam, the gaseous state of water, is widely used in various industries for it’s unique properties such as it’s ability to transfer heat and energy. It’s produced when water is heated to it’s boiling point and the liquid transforms into a gaseous state. At sea level, the boiling point of water is 100°C(212°F), but it’s important to note that this temperature isn’t the maximum temperature that steam can reach.
Superheated steam, also known as dry steam or saturated steam, is steam that’s been heated above it’s boiling point at a specific pressure. By introducing additional energy to the water molecules, the temperature of the steam can be increased well above 100°C. This superheated steam has unique properties, and it’s commonly used in industries such as power and energy, food processing, and chemical manufacturing.
Despite it’s advantages, superheated steam can also be dangerous if not handled properly. The steam can cause severe burns if in contact with the skin, and at high temperatures, it can ignite combustible materials.
Comparing the Properties and Uses of Steam to Other Heat Transfer Fluids Like Oil and Air
- Steam has a higher specific heat capacity compared to oil and air
- Steam is a gas at normal atmospheric pressure and temperature, while oil and air are liquids and gases respectively
- Steam is mainly used for heating, whereas oil is used for heating and cooling, and air is used for cooling and ventilation
- Steam transfers heat through latent heat of vaporization, while oil and air transfer heat through conduction and convection respectively
- Steam can cause burn injuries if not handled properly, while oil and air don’t pose such risks
Source: Superheated steam – Encyclopedia Britannica
As we delve deeper into the process of steam distillation, it’s essential to understand the various factors that affect this technique’s outcome. While some of these factors are intrinsic, others are external and can be controlled to some extent. Factors like the natures of crude oil, temperature, and pressure can significantly impact the outcome of steam distillation. In this article, we’ll explore these factors in detail and try to understand their effect on the overall steam distillation process.
What Are the Factors Affecting Steam Distillation?
However, the natures of crude oil may vary and can affect the distillation rates depending on the oil source and it’s properties. For instance, heavier crude oil has more complex structures and more hydrocarbon molecules per unit volume compared to lighter crude oils, which are easier to distill and require lower temperatures and pressures.
The presence of impurities such as sulfur, nitrogen, and metals can also affect the efficiency of steam distillation. These impurities may form compounds that require higher temperatures and pressures to be separated from the crude oil, resulting in longer processing times and lower yields. Additionally, impurities can corrode the distillation equipment, causing damage to the equipment and reducing it’s lifespan.
Adequate steam injection and proper control of the steam-oil ratio is necessary to ensure efficient and effective distillation. If the steam-to-oil ratio is too low, the temperature of the crude oil won’t reach the boiling point, resulting in incomplete distillation. On the other hand, excessive steam injection can cause flooding, leading to less efficient distillation and potential damage to the distillation equipment.
Furthermore, the distillation column design and equipment configuration are crucial factors in determining the efficiency of steam distillation. The design of the column should be optimized for the specific crude oil being processed and the desired end-product. Proper positioning of trays, reboilers, and condensers is essential for the effective separation of the different components in the crude oil.
These parameters must be optimized to achieve maximum efficiency and desired product quality. For example, adjusting the reflux ratio can improve the separation of components in the distillation column by reducing the amount of lower boiling point components in the overhead product.
Understanding the natures of crude oil, external operating conditions, and equipment configurations is crucial in optimizing the efficiency and quality of the distillation process. By carefully controlling all of these factors, distillation can be an effective way to separate and purify the different components of crude oil for various industrial applications.
Conclusion
The precise temperature control is an essential aspect of this process as it affects the yield and quality of the final product. However, maintaining a temperature range between 140° F and 212° F (60° C and 100° C) is generally considered optimal.