The Glycerine leak in a pressure gauge refers to the escape or seepage of glycerine from the device. Pressure gauges often use glycerine as a damping fluid to stabilize the pointer for more accurate readings. The gauges are frequently filled with this liquid for its beneficial properties, like reducing pointer vibration or protecting the internal parts from harsh external environment. However, if a leak occurs, the glycerine escapes, which can compromise the device’s functionality and accuracy. It can be caused by several factors, including faulty seals, overpressure, or physical damage to the gauge. It’s essential to address such leaks promptly to ensure the gauge’s reliability and longevity.
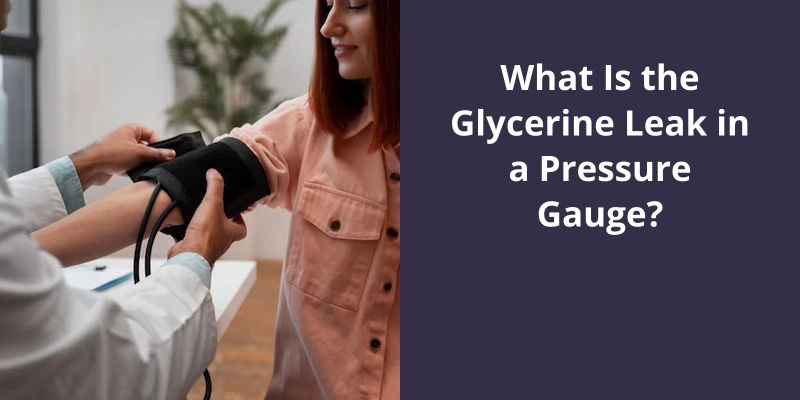
What Is the Liquid Inside the Pressure Gauge?
Pressure gauges are an integral part of many industries, including manufacturing, oil and gas, and healthcare. They’re used to measure the pressure of fluids and gases in various settings. These gauges come in different types, including digital and liquid-filled gauges. In a liquid-filled gauge, the primary component is the liquid, which is responsible for the dampening of vibrations that may affect the gauges accuracy.
When it comes to the most common liquid in a liquid-filled pressure gauge, glycerin tops the list. Glycerin is a sugar alcohol that’s colorless and odorless. It’s widely used in the food and pharmaceutical industries, as well as in personal care products due to it’s moisturizing properties. Additionally, glycerin is widely used in the production of dynamite, among other industrial applications.
One of the primary reasons for the popularity of glycerin in liquid-filled pressure gauges is it’s affordability. Compared to other liquids used in these gauges, such as silicone oil, glycerin is relatively cheap. Additionally, glycerin has excellent lubricating properties, which means that it can help reduce friction between the gauges moving parts. This property is crucial in high vibration settings, as it helps prolong the gauges lifespan.
Another important property of glycerin is it’s viscosity. The viscosity of a liquid refers to it’s resistance to flow. Glycerin is a highly viscous liquid, which means that it flows slowly. This property is critical in liquid-filled pressure gauges, as it helps to dampen vibrations and shockwaves that may affect the gauges accuracy. This, in turn, leads to more precise readings and a longer lifespan for the gauge.
For example, it’s a high boiling point and a low freezing point. This means that even in extreme temperatures, glycerin won’t boil or freeze, ensuring that the gauge remains accurate. Additionally, glycerin is non-toxic and non-reactive, making it safe for use in a wide range of settings, including those that involve contact with food or pharmaceuticals.
What Are the Different Types of Pressure Gauges and How Do They Work?
Pressure gauges are devices that measure the pressure of liquids and gases. There are several types of pressure gauges, including bourdon tube, diaphragm, and capsule gauges. Bourdon tube gauges use a curved tube that straightens as pressure increases, while diaphragm gauges use a flexible diaphragm that deforms under pressure. Capsule gauges use two diaphragms that are welded together to form a sealed capsule. All of these gauges work by translating the pressure of the fluid or gas into a mechanical displacement that can be read on a dial or gauge face.
Now that we understand the benefits of using liquid-filled pressure gauges, it’s important to explore the differences between oil-filled and dry pressure gauges. While both types of gauges have their advantages, they also have distinct differences that could affect the performance of your equipment. Let’s take a closer look at the pros and cons of each type of gauge and how to determine which one is right for your needs.
What Is the Difference Between Oil Filled and Dry Pressure Gauges?
The glycerine provides a viscous cushion that dampens the pressure effects from the gauges movement, ensuring highly accurate and steady readings. Oil-filled pressure gauges are primarily used in industrial applications that require a higher degree of accuracy. These gauges are generally filled with silicone oil, which is chemically stable and can withstand extreme temperatures and pressures.
Another significant difference between the two gauges is their construction. Liquid-filled gauges are designed with a sealed environment that accommodates the liquid, while dry gauges have a basic mechanism with no fluid. That being said, oil gauges have a more robust build and can withstand high shock and vibration environments, making them ideal for heavy-duty applications.
When it comes to maintenance and longevity, liquid-filled gauges require regular filling to ensure they remain functional. This is because, over time, the glycerine can dry up, lose viscosity, or evaporate, which can lead to inaccurate readings. Dry gauges, on the other hand, are more durable and low maintenance, requiring less frequent calibrations.
One significant advantage of using liquid-filled pressure gauges is their readability in low-light environments. The glycerine inside the gauge can help reflect light, making the readings more visible. Additionally, if a gauge is used in a corrosive environment, the liquid can help protect the internal parts from damage.
Applications Where Oil-Filled Pressure Gauges Are Most Commonly Used
Oil-filled pressure gauges are widely used in applications that involve high levels of vibration or pulsation, as well as those that require accurate readings in harsh environments with high temperatures or corrosive substances. Some common applications include hydraulic systems, compressors, pumps, and engines. The oil filling helps to dampen the effects of vibration and pulsation, while also providing lubrication and protection against corrosion.
Source: Liquid-Filled vs. Dry Pressure Gauges – PRM Filtration
It’s essential to ensure that pressure gauges are accurate and functioning correctly in various applications. A faulty pressure gauge can lead to various complications, ranging from inaccuracies to hazardous conditions. In this article, we will explore the effects of inaccurate pressure gauges and the measures to maintain their accuracy.
What Will Happen if the Pressure Gauge Is Not Accurate?
The consequences of an inaccurate pressure gauge can be significant. If pressures aren’t being monitored correctly and accurately, it can lead to potential safety issues in an industrial and manufacturing environment. This can have potentially severe consequences for personnel and the environment.
In some cases, this can result in production downtime leading to lost revenue or even in product recalls. These issues then lead to additional costs, lost productivity, and headaches that can have a serious impact on a companys bottom line.
An imprecise pressure gauge also has implications for product quality and performance. When pressure gauges fail to perform accurately, there’s a risk that industrial processes can be destabilized, leading to inconsistencies and variations in product quality and performance. This can impact downstream processing, compound errors, and produce downstream processing challenges, as well as impacts to upstream processes.
Another issue resulting from inaccurate pressure gauges is wasted energy. Suppose a system is running with inaccurate pressure readings. In that case, it’s easy to over-exert the system, which can lead to overheating and increased wear and tear on production lines. Therefore, to avoid unnecessary energy consumption, regular pressure gauge calibration is essential.
Types of Pressure Gauges and Their Specific Uses in Different Industries
- Bourdon tube pressure gauge – used in chemical, petrochemical, and oil and gas industries
- Diaphragm pressure gauge – used in food and beverage industries
- Capsule pressure gauge – used in pharmaceutical industries
- Digital pressure gauge – used in pharmaceutical, chemical, and food industries
- Differential pressure gauge – used in HVAC, clean room, and laboratory applications
- Magnetic pressure gauge – used in food processing and pharmaceutical industries
- Manometer pressure gauge – used in research and development and laboratory applications
- Spring pressure gauge – used in automotive and mechanical engineering industries
- Vacuum pressure gauge – used in vacuum packaging, refrigeration, and HVAC industries
Now that we’ve discussed the purpose of filling a pressure gauge with liquid, it’s important to address the question of whether or not water should be used. This debate has been a topic of discussion among professionals in the field, with different opinions and arguments for both sides. Let’s take a closer look at the arguments for and against using water in a pressure gauge.
Should a Pressure Gauge Have Water in It?
However, using water as a liquid filling isn’t recommended. The reason being, water is corrosive in nature, and it can lead to rusting and corrosion in the internals of the gauge. This results in shortening the lifespan of the gauge, and sometimes it can even cause the gauge to fail, which is why most manufacturers use glycerine or silicone as a filling material instead of water.
Furthermore, water-filled gauges are also less accurate, as the temperature changes can cause the water to expand and contract, leading to changes in readings. In addition, water-filled gauges aren’t suitable for applications in freezing temperatures, as the water can freeze and cause the gauge to fail or burst.
What Are the Advantages and Disadvantages of Using Glycerine and Silicone as Filling Materials for Pressure Gauges?
Using glycerine and silicone as filling materials for pressure gauges have their own advantages and disadvantages. Glycerine is less expensive and provides damping for the gauge, but can degrade and turn color over time. Silicone is more durable and resists temperature changes, but is more expensive and may not provide as much damping as glycerine.
Conclusion
It’s actually a normal occurrence with glycerine-filled pressure gauges, as the air bubble serves an important purpose in maintaining the flexibility of the diaphragm. This feature is essential to the proper functioning and accuracy of the pressure gauge.