Seal Came Off With Cap – A Troubleshooting Guide. In the world of product packaging, it isn’t uncommon for consumers to encounter sealing issues, particularly when it comes to the caps and lids of various containers. One such frustrating experience is the scenario where the seal comes off along with the cap, leaving users puzzled and seeking a solution. Whether you’re dealing with food containers, medication bottles, or any other items that require a sealed cap, this comprehensive guide will equip you with the necessary knowledge to understand the potential causes behind this phenomenon and tackle it effectively. From examining the quality of the seal to exploring alternative closure methods, we will dive into various troubleshooting techniques that will empower you to resolve this pesky issue.
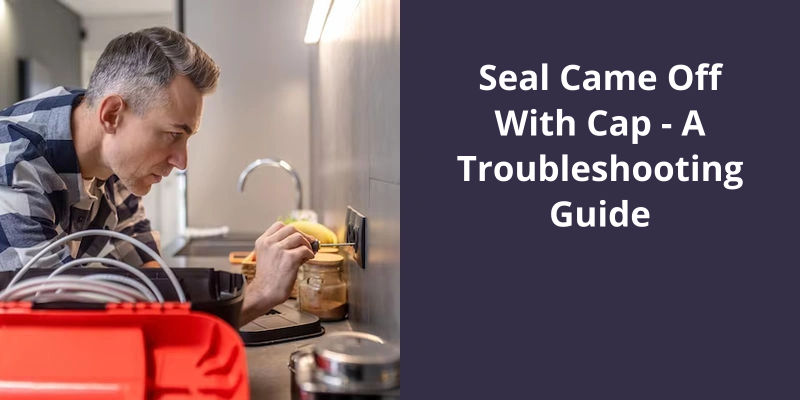
How Does an Induction Cap Sealer Work?
An induction cap sealer is a vital piece of equipment used in various industries for sealing containers with foil liners. It employs a unique electromagnetic field to ensure a secure and hermetic seal. The system consists of a sealing head that generates the necessary electromagnetic energy and a power supply that provides the required electricity.
When the cap is placed on the container, the sealing head activates and produces the electromagnetic field. This field interacts with the foil liner inside the cap, causing it to heat up rapidly. The induction process heats only the foil liner and not the cap or container, ensuring efficient and localized heating.
As the foil liner reaches it’s melting point, the polymer coating on the inner-seal softens and becomes sticky. The pressure applied by the cap on the containers lip allows the softened inner-seal to bond securely to the rim of the container. This bond, combined with the heat generated by the induction cap sealer, forms a hermetic seal that prevents leakage, contamination, and tampering.
In addition to providing a strong seal, induction cap sealers also offer tamper-evident packaging. Once the foil liner has been bonded to the rim of the container, any attempt to remove the cap will result in noticeable damage to the seal, indicating tampering. This feature is crucial in industries where product integrity and consumer safety are paramount.
It’s electromagnetic heat generation and precise control make it a popular choice for industries requiring efficient, tamper-evident sealing.
The History and Evolution of Induction Cap Sealers
The history of induction cap sealers dates back to the 1960s when they were first introduced as a revolutionary sealing solution for airtight packaging. Initially, induction sealing technology was used primarily in the pharmaceutical and food industries to prevent tampering and ensure product integrity.
Over the years, induction cap sealers have evolved and become increasingly advanced. Today, they’re widely used in various industries, including beverages, cosmetics, and chemicals. The primary function of induction cap sealers is to create a hermetic seal between the cap and container, preserving the freshness and preventing leakage of the packaged product.
Induction sealing works by applying an electromagnetic field to a foil liner bonded to the container’s opening. The heat generated by the induction field melts the foil, creating a secure, tamper-evident seal. This method offers many benefits, including improved product shelf life, enhanced safety, and reduced risk of contamination.
Modern induction cap sealers come in different types and sizes, ranging from handheld units for small-scale applications to fully automated systems for high-speed production lines. These sealers offer advanced features like adjustable power settings, digital temperature controls, and precise sealing time programming.
In recent years, advancements in induction sealing technology have focused on improving efficiency and productivity. For instance, new systems incorporate sensors and intelligent controls to maximize sealing accuracy and minimize energy consumption. Additionally, manufacturers have developed specialized sealing materials and liners to ensure compatibility with a wide range of container materials.
As the packaging industry continues to evolve, induction cap sealers play a crucial role in meeting the demands for secure and convenient packaging. With ongoing developments and innovations, these sealers are likely to further enhance sealing efficiency and flexibility in the future.
Moving beyond the conventional means of packaging, cap seals have emerged as a crucial component in ensuring the safety and integrity of various containers. These seals, made of aluminum, plastic, or compound materials, are meticulously placed on the opening of vials, bottles, jars, and more. With their ability to provide a hermetic and watertight seal, cap seals play a vital role in safeguarding the contents within while also extending the shelf life of products.
What Is Cap Seal in Packaging?
A cap seal plays a crucial role in packaging, ensuring the integrity of various products. It acts as a protective barrier between the contents of a container and the external environment. Typically, a cap seal is a thin film made of materials like aluminium, plastic, or other compound materials. It’s positioned on the opening of containers such as vials, bottles, jars, pill bottles, or jugs.
The primary purpose of a cap seal is to provide a hermetic and watertight seal, preventing any leakage or contamination. It ensures that the product remains fresh, safe, and free from any external impurities. By forming a tight seal, the cap seal helps to maintain product quality and extend it’s shelf life. It also prevents any tampering or unauthorized access, preserving the consumers trust in the product.
In addition to it’s protective functions, a cap seal can also serve as a promotional tool. Manufacturers often utilize cap seals as a platform for printing branding information, logos, or promotional messages. This enhances product visibility and creates a unique identity for the brand.
There are various types of cap seals available, depending on the specific requirements of the packaging. For instance, induction seals are commonly used for products like pharmaceuticals, food items, and chemicals. These seals are applied using heat induction technology, creating a secure and tamper-evident closure.
It acts as a protective barrier against leakage, contamination, and tampering.
The Manufacturing Process of Cap Seals This Topic Can Provide Insights Into How Cap Seals Are Manufactured. It Can Discuss the Materials Used, the Machinery and Equipment Involved, and the Quality Control Measures Taken During the Manufacturing Process.
The manufacturing process of cap seals involves several steps to ensure their quality and functionality. First and foremost, the materials used for cap seals need to be carefully selected. Typically, these materials are chosen for their durability and resistance to various environmental conditions, such as moisture, heat, and chemicals.
Once the materials are chosen, they go through a molding process. This process typically involves heat and pressure to form the materials into the desired shape of the cap seal. The machinery and equipment used in this process are designed to ensure precise molding and sealing.
Quality control measures play a crucial role in the manufacturing process of cap seals. Inspections and tests are conducted to check for any defects or imperfections in the seals. This helps in identifying and rectifying any issues before the cap seals are shipped out to customers.
Overall, understanding the manufacturing process of cap seals can provide valuable insights into the complexities and attention to detail required to produce high-quality caps that properly seal and protect the contents of bottles and containers.
Cap seals are specially designed seals that offer a low friction seal for dynamic reciprocating applications. They consist of a plastic cap that provides a seal against the dynamic sealing face, while an O-ring is used to energize the plastic cap. These seals are primarily used in applications where the seal operates in a static environment, providing effective sealing while reducing friction and ensuring smooth movement.
What Is a Cap Seal?
A cap seal is a crucial component in dynamic reciprocating applications. It ensures a low friction seal, allowing smooth movement and preventing leakage. This seal consists of a plastic cap and an O-ring that work together to provide an effective seal in a dynamic sealing face.
It’s designed to fit tightly and securely, preventing any undesirable leakage of fluid or gas. The material used for the cap is carefully selected to withstand the harsh conditions of the application, ensuring durability and long-lasting performance.
To further enhance the sealing capability of the cap, an O-ring is utilized. It’s positioned in a static environment, allowing it to exert constant pressure on the cap, thereby increasing it’s sealing effectiveness.
However, there may be instances when the seal fails, and the cap comes off. This can occur due to a variety of reasons, such as excessive pressure, improper alignment, or worn-out components. Troubleshooting such issues requires a systematic approach, including inspecting the cap seal, checking for any damage or misalignment, and evaluating the operating conditions.
It offers a low friction seal through the use of a plastic cap and an O-ring. When functioning properly, it prevents leakage and ensures the efficiency of the system. However, in case of a seal failure, troubleshooting becomes necessary to identify and rectify the issue.
When it comes to products or documents, breaking a seal signifies the act of unsealing or opening them. This action can indicate a breach in the integrity of the seal, warranting attention and potential consequences.
What Does It Mean if a Seal Is Broken?
When a seal is broken, it signifies the disruption of an originally secure and protected state. This can apply to various contexts, including personal, legal, or mechanical situations. In the case of opening a sealed letter, breaking the seal is akin to breaching the trust and privacy associated with the sealed contents. It often implies disregarding societal norms or boundaries.
Moreover, the concept of a broken seal holds significance in legal contexts. Many official documents or contracts require a seal to validate their authenticity and ensure tamper-proof conditions. Therefore, breaking such a seal could invalidate the document or question it’s legal standing, potentially leading to legal consequences or challenges.
For instance, if a seal on a container or a bottle comes off with the cap, it indicates a problem with the packaging, which could lead to leaks, contamination, or spoilage of the contents.
To rectify this issue, a troubleshooting guide for dealing with a broken seal that comes off with the cap becomes necessary. Such a guide should provide step-by-step instructions on how to properly handle the situation, ensuring the integrity of the product and preventing any potential harm or inconvenience caused by the broken seal.
The Legal Implications of Breaking a Seal: This Topic Could Delve Deeper Into the Legal Consequences and Ramifications of Breaking a Seal, Such as the Invalidation of Contracts or the Potential for Lawsuits.
When a seal is broken, it can have various legal implications depending on the context. In some cases, breaking a seal may render a contract or agreement null and void. This means that parties involved may lose any legal protection or rights outlined in the contract. Furthermore, breaking a seal could potentially result in legal liability and open the door for lawsuits. It’s important to understand the specific terms and conditions associated with a seal before taking any action that may result in it’s breaking.
If you discover that the seal on your container is broken, it’s essential to take immediate action. Start by capturing photos of the seal (if one is present) and the container itself. Next, it’s crucial to contact your carrier, freight forwarder, and insurance company right away. However, refrain from opening the container until a representative from the shipping line is present. While waiting, continue documenting the situation by taking photos of the contents once the container is finally opened.
What to Do if Container Seal Is Broken?
If you’ve encountered a situation where the seal of a container has come off with the cap, it’s important to take immediate action and follow a troubleshooting guide for a smooth resolution. The first step is to document the evidence by taking clear and detailed photographs of both the broken seal (if any) and the container itself. This will serve as crucial evidence to support your claim later on.
After documenting the situation, the next step is to promptly contact your carrier, freight forwarder, and insurance company. Inform them about the issue and provide them with the photographic evidence. It’s important to notify them immediately to ensure a timely resolution and to initiate the necessary investigations.
While it may be tempting to open the container to assess the contents, it’s crucial to wait until a representative from the shipping line is present. Their presence will ensure that the opening process is properly documented, witnessed, and can provide any necessary guidance. Opening the container without proper supervision may jeopardize the integrity of the investigation and your claim.
Throughout the process, it’s essential to continue taking photographs of the contents of the container once it’s been opened. This documentation should be done in a detailed and systematic manner, capturing the condition and order of the items as they’re found. These additional photographs will serve as important evidence to support your claim and provide a comprehensive picture of the situation.
By following this troubleshooting guide, you can ensure that the necessary steps are taken to address the issue effectively.
How to File a Claim With the Shipping Line, Freight Forwarder, and Insurance Company After a Broken Container Seal.
If you’ve experienced a broken container seal during shipping and need to file a claim, here’s a step-by-step guide to help you through the process:
1. Contact the shipping line: Start by reaching out to the shipping line responsible for transporting your goods. Provide them with detailed information about the broken seal and any accompanying damage. They’ll guide you on their specific claim procedures and documentation requirements.
2. Notify the freight forwarder: If you used a freight forwarder to handle the shipment, inform them about the broken seal and the related damages. They can assist you in coordinating with the shipping line and provide additional support throughout the claims process.
3. Gather evidence: Collect all relevant evidence to support your claim. This may include photographs of the broken seal, packaging, and any damaged items. Maintain copies of shipping documents, invoices, and any other paperwork that can support your case.
4. File a claim: Prepare a formal claim letter explaining the incident, including all relevant details and supporting evidence. Submit this document to the shipping line, along with any required forms or paperwork they may have specified. Keep copies of all documents for your records.
5. Contact the insurance company: If you’ve cargo insurance, contact your insurance provider to initiate the claims process with them. Ensure that you provide all required information and documentation to support your claim. They’ll guide you through their specific procedures and requirements.
6. Follow up regularly: Stay in touch with both the shipping line and the insurance company to monitor the progress of your claim. Be persistent in requesting updates and provide any additional information they may require promptly.
Remember to familiarize yourself with the specific procedures and requirements of the shipping line, freight forwarder, and insurance company involved in your shipment. By actively engaging in the claims process and providing thorough documentation, you increase your chances of a successful resolution.
Source: What happens if your container seal has been broken
Conclusion
It can be attributed to various factors such as improper storage, excessive pressure build-up, or manufacturing defects. By employing preventive measures like proper storage techniques, ensuring appropriate pressure release, and inspecting product packaging, one can minimize the occurrence of this problem. Additionally, being aware of alternative sealing methods and seeking professional assistance when necessary can contribute to resolving the issue. Ultimately, this troubleshooting guide equips individuals with valuable knowledge to address the seal coming off with a cap, ensuring product integrity and customer satisfaction.